What is NextGen TSR?
NextGen Tundish Spray Robot is a game-changer in the industry, designed to take tundish fleet performance to the next level. With our expertise in engineering technology and Tundish refractories, we have developed the NextGen Tundish Spray Robot that is safe, reliable, and consistent in its performance.
Key features
A few of the key advances of the Tundish Spray Robot Solution include:
- New KUKA robot
- New cage and dual spray mixer station design
- New operator-friendly Vesuvius interface
- Enhanced Vesuvius Robot code
...and many more.
All these improvements give operators maximum control and flexibility for the optimization of spray mass installation in a wide range of spraying routines and endless tundish repair scenarios.
Contact our specialist to find out how your Tundish Bay can benefit from the solution.
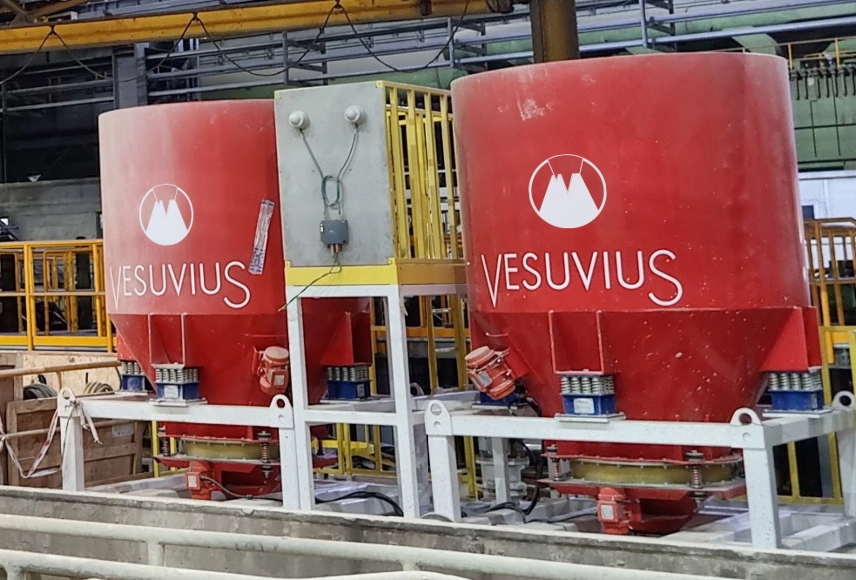

Safe Design
Our NextGen TSR is designed with safety in mind. The robot is arranged inside a fully enclosed heavy-duty steel frame with lifting trunnions matching those on the tundish. Access doors are electrically interlocked with the robot fence circuit to prevent human interaction with the robot during operation. The cage allows completely safe viewing of spraying operation from close proximity creating a safe zone between the tundish and operator. The Control cabinet and robot controller are embedded on robot cage and sealed for climate control.

Superior Repeatability
The NextGen TSR is designed to provide a consistent spray pattern and repeatable spray weights, which is essential for the proper application of materials, leading to improved tundish life and performance. No manual applicator can match the repeatability of the NextGen TSR.

Faster Lining
With the NextGen TSR, there is a significant decrease in tundish preparation cycle times independent of the operator's experience. After application of the “flash coat” on a hot tundish, the robot can continue spraying the subsequent coats almost independent of Tundish internal temperature. This feature saves time compared to manual lining, where operators typically wait for the steam to die down before going in again to spray the subsequent coats.

Laser Setting & Automated Spray
The laser guided tundish furniture setting system ensures that all surfaces within the tundish are properly positioned for optimal robotic spraying. This feature is designed to guide the operator for perfect location of all castable furniture.
Our spray machine is completely automated, including processes such as water addition, slurry temperature control, feeding rate, and application of the desired thickness. This ensures a consistent material is delivered to the robot according to quality standards.

Zone Spray & Zero Waste
Vesuvius NextGen TSR offers maximum flexibility for the optimization of spray mass installation in a wide range of different tundish scenarios. By controlling material usage, we reduce material volumes above the slag line and in corners, resulting in a reduction in wasted material. This feature is done by using the zoning factor, which is key to the NextGen TSR.
Our automated system provides an instant mix and a 24/7 control of material and process based on the input data and continuous cycles according to tundish bay workload, resulting in the minimum material waste in the plant at the end of the day.

Portable Design
Our robot is assembled inside a fully enclosed heavy steel frame with a trunnion, making it easy to move in the tundish bay and manage different tundish types/designs with one robot. We have references globally where customers are managing 2 or 3 different tundish designs serviced by a single Vesuvius robot.
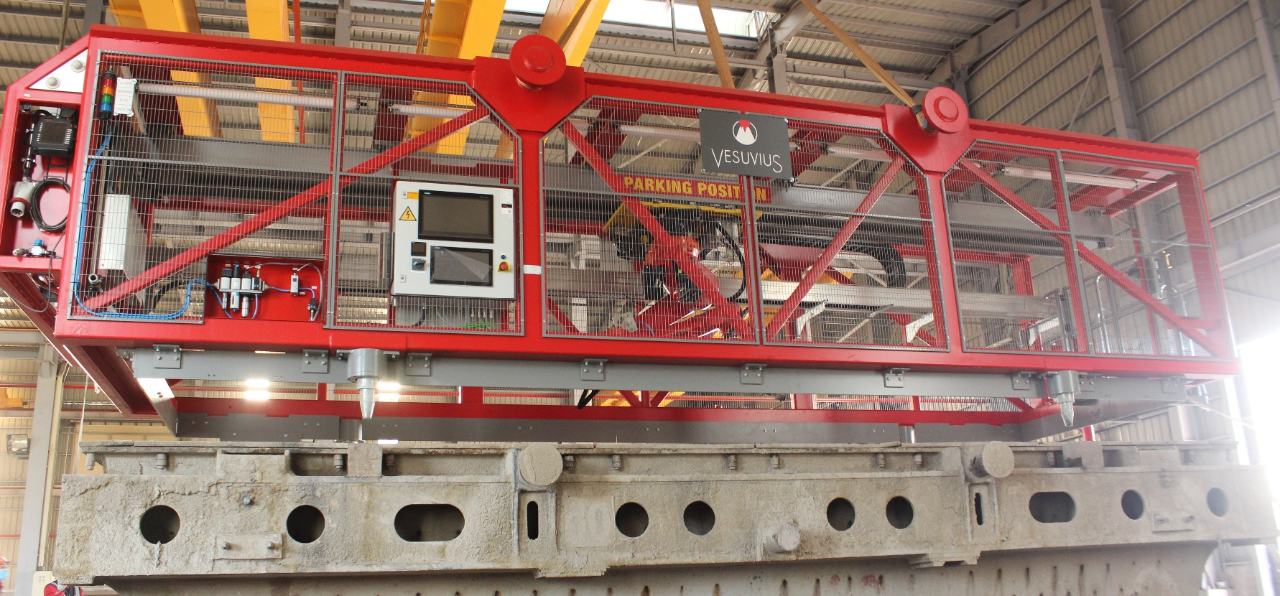