Tundish Dry-Vibratable Robot (TDVR)
Full automatic Dry-Vibratable application for tundish
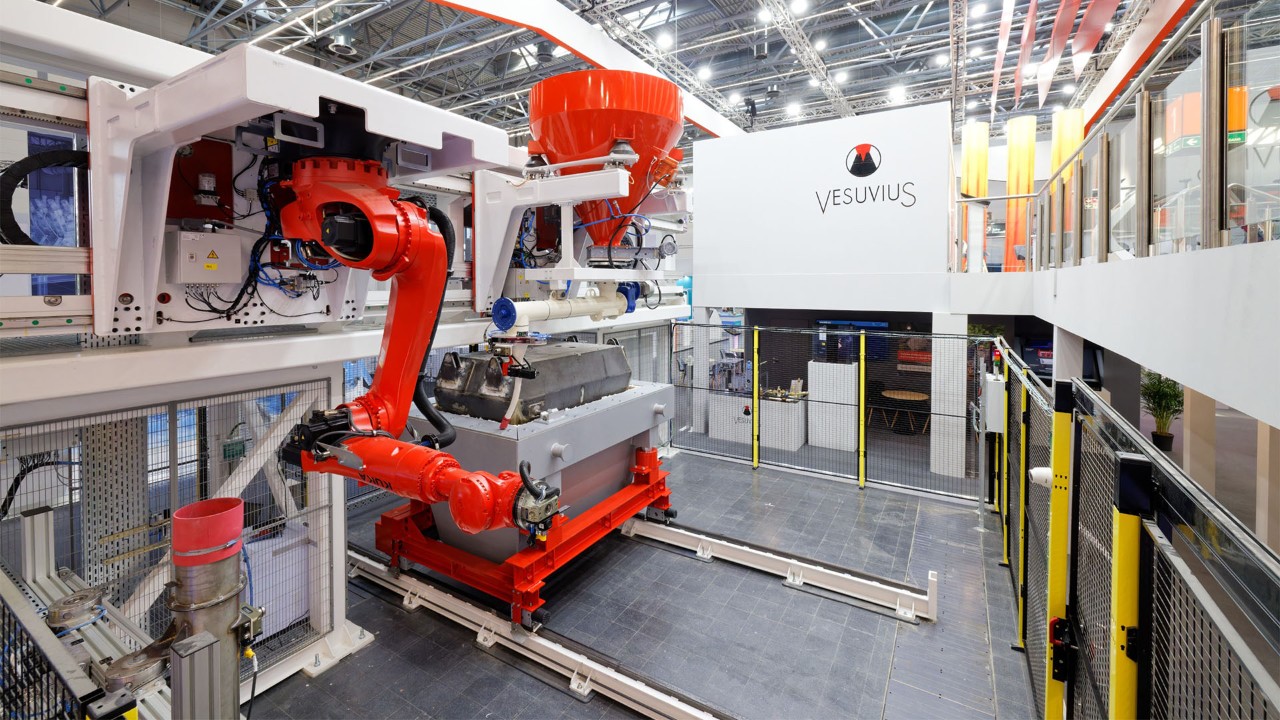
Tundish Dry-Vibratable Robot (TDVR) is the most recent Vesuvius groundbreaking innovation. This advanced robot presents a novel approach to the automatic application of a dry working lining in a tundish, offering remarkable benefits to our valued customers.
The Tundish Dry-Vibratable Robot marks a significant milestone in tundish technology, introducing an automated solution for layering the working lining. By employing a state-of-the-art robot, this revolutionary system reduces the need for manual labor in environments characterized by increased dust levels, high temperatures, and potential safety hazards.
NextGen TSR
Safe, repeatable and reliable performance, keeping your tundish fleet performing at a higher level
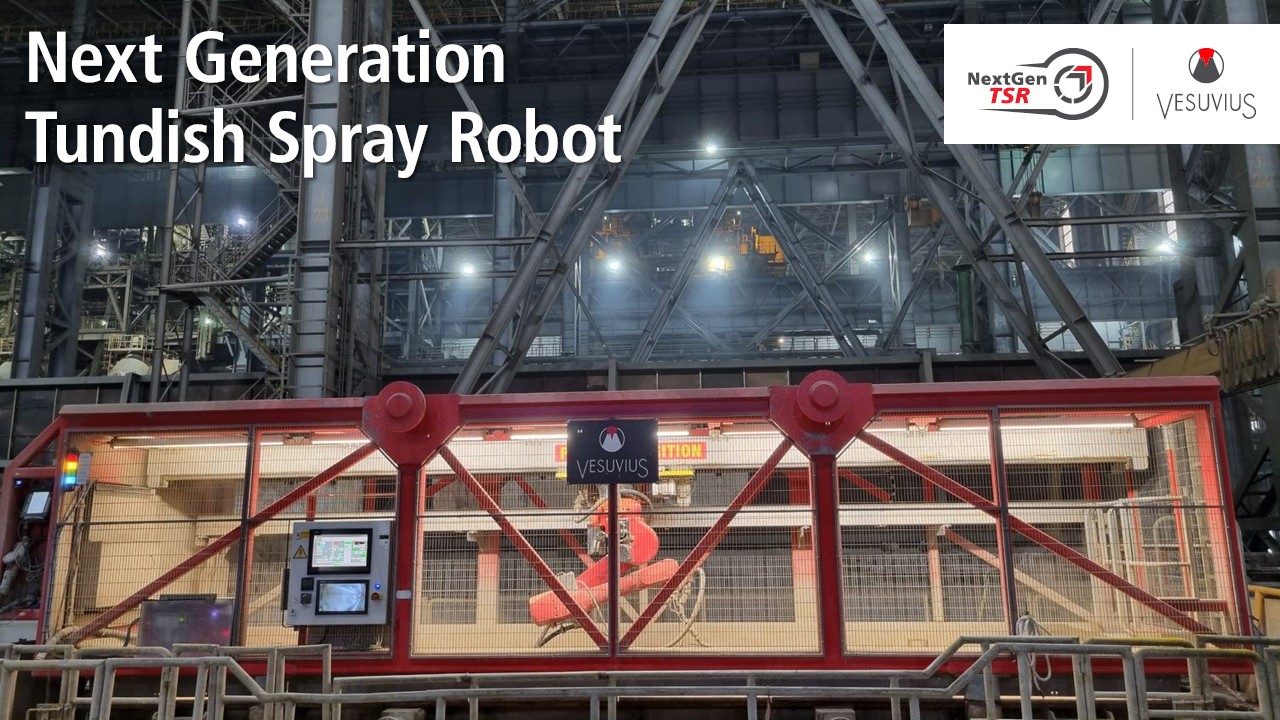
NextGen TSR is a groundbreaking advancement in the industry, specifically designed to elevate tundish fleet performance. Developed by Vesuvius, a leader in engineering technology and tundish refractories, the NextGen Tundish Spray Robot offers safety, reliability, and consistent performance. Some key features include:
- New KUKA Robot: The NextGen TSR employs an advanced KUKA robot for precise and efficient spraying.
- Enhanced Design: The robot operates within a fully enclosed, heavy-duty steel frame, ensuring safety during operation. Access doors are interlocked to prevent human interaction during spraying.
- Superior Repeatability: The robot consistently delivers a uniform spray pattern and repeatable spray weights, crucial for optimal material application and improved tundish life.
- Faster Lining: The NextGen TSR significantly reduces tundish preparation cycle times, independent of operator experience. It can continue spraying subsequent coats even at high tundish temperatures.
- Laser-Guided Furniture Setting: A laser system ensures precise positioning of tundish furniture, enhancing overall spray quality.
- Automated Spray Process: The robot handles water addition, slurry temperature control, feeding rate, and thickness application, ensuring consistent material delivery.
- Zone Spray & Zero Waste: Material usage is optimized, reducing waste above the slag line and in corners.
The NextGen TSR revolutionizes tundish maintenance, offering efficiency, safety, and improved performance for steelmaking processes.