ANTERIS Series Laser Contouring System (LCS)
Laser Contouring Systems are instruments that determine the thickness of refractory lined metallurgical vessels (BOF, Q-BOPs, AOD, EAF, Ladle or Torpedo Ladle and essentially any metallurgical vessel). Such measurement is achieved by first measuring the distance from a known location to a large number of points distributed over the interior of the refractory surface. If the position of the system is known relative to the vessel being measured, these distance measurements can mathematically be converted to lining thickness.
Thousands of range measurements are typically made when scanning a metallurgical vessel. Using the ANTERIS laser scanner, these measurements are acquired at a data rate of up to 300,000 points per second. These data are subsequently combined to yield the overall internal refractory profile. Data presentation includes contour maps, individual radial slices, and horizontal slices that clearly illustrate the measured contour compared against the as-bricked profile.
The ANTERIS product range offers many installation alternatives to retrofit existing facilities to improve safety, offer superior refractory thickness management performance, and a project management philosophy that aims to achieve seamless integration to the existing facilities.

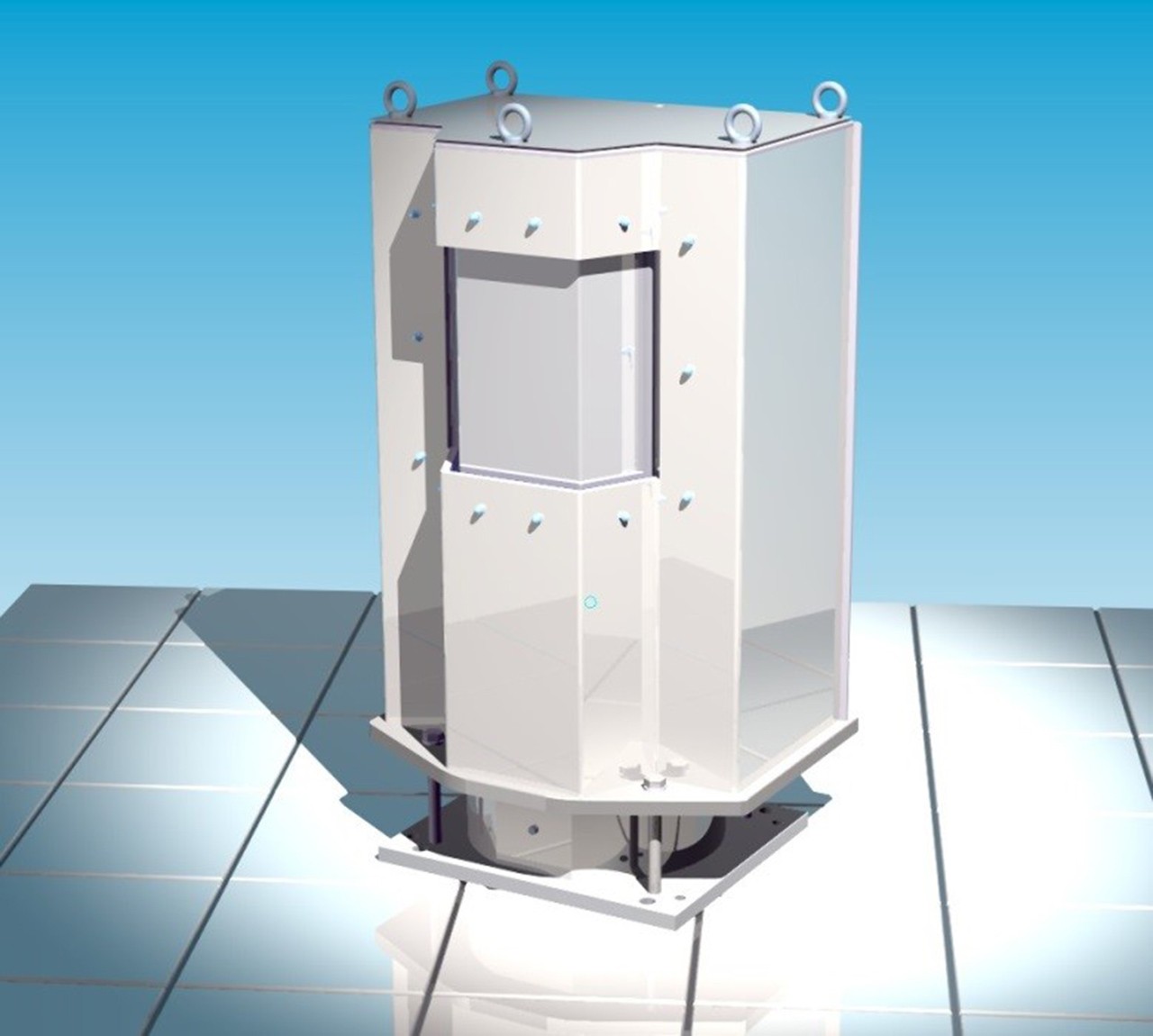
Theory of Operation
The LCS instrument is a high-speed laser range finder that measures distance to-target using time-of-flight laser range finding. A laser is pulsed rapidly over a short time interval (nanoseconds). The pulse of energy (photons of light) is detected by a detector that creates a voltage pulse that is introduced to a counter to initiate counting. This pulse energy is also directed to the face of a rotating mirror (the fast-scan mirror). The fast scan mirror re-directs the energy out of the front window of the scanner, where it travels to and is reflected from a far-field surface. The reflected energy is again reflected by the fast scan mirror face to a collection lens. The collection lens focused the energy onto the face of a detector that converts the light energy into a voltage pulse. The pulse is amplified in the electronics of the ANTERIS laser and is directed to the counter to stop counting. The count value multiplied by the known speed of light returns the desired range value.
This process is repeated 120,000 times per second as both the fast-scan mirror is turning, and as slow scan turret rotation occurs. As both elements rotate, the pulse energy emitted by the laser is swept over the scene of interest, and a family of range values is collected that defines distance to the points identified in the scene. Spacing between points is defined by the resolution of the scanner. Since both range and intensity (returned signal strength) is included in the measured signal, a false-colored image can be created of the scanned scene of interest.
ANTERIS 300 range
The PROCESS METRIX product line provides our customers with the only laser scanner developed specifically for molten metal applications. The highly reliable TDS-300 scanner, incorporates state-of-the-art technology to provide lining thickness information that defines the refractory condition of ladles, converters, AOD’s, EAF’s and Q-BOP’s.
Product range and Integration in the Steel plant.
The refractory thickness measurement product range has been designed to offer the best integration solution to the steel plant. The ANTERIS 300 range products cover a wide range of possible applications defined by the existing layout. All steel plants are different: no single solution can cover all cases. Strengthened by the knowledge acquired through decades of experience retrofitting existing facilities, Vesuvius has developed a wide range of solutions for all vessels to lower integration costs and maximize thickness measurement performance.
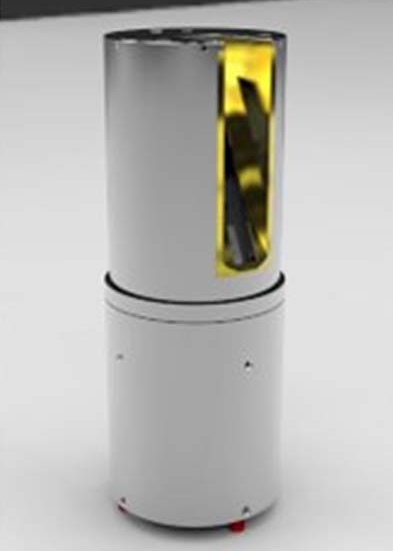
Performance
Our customers demand performance, particularly in the ability to detect small features (cracks) in the lining profile. This can only be done with a laser beam that has a beam diameter equal to or less than the minimum feature size. Vesuvius has developed the ANTERIS laser scanner with a small, 3.6 mm diameter laser beam. In this geometry, the ANTERIS laser can provide outstanding surface topology data that defines the smallest of features on the refractory surface.
- Small (3.6mm) beam diameter for outstanding surface topology data capture,
- High accuracy (±1.8mm @1σ) scanning,
- Fast – Full vessel scan in 10-15s at high resolution,
- Optional integrated two-color pyrometer
- Robust – suitable for the mill environment and the heat loads imposed during scanning high temperature surfaces,
- Eye safe laser wavelength,
- -45° to +65° vertical scan angle, 0-360° horizontal scan angle
ANTERIS 300r
Robotic arm
For most refractory thickness measurement in ladles, a simple installation can be found that does not require much civil works. However, in certain cases, handling solutions are needed to go around retrofit challenges, such as:
- Laser head is located over a ladle and must clear the crane hook
- A single laser head must be multiplexed and cover multiple ladle stations
- In EAF cases, the laser must be brought over the furnace when the furnace roof is removed.
In almost all cases Vesuvius can offer a custom-made and flexible solution with a robotic arm design and turn-key project.
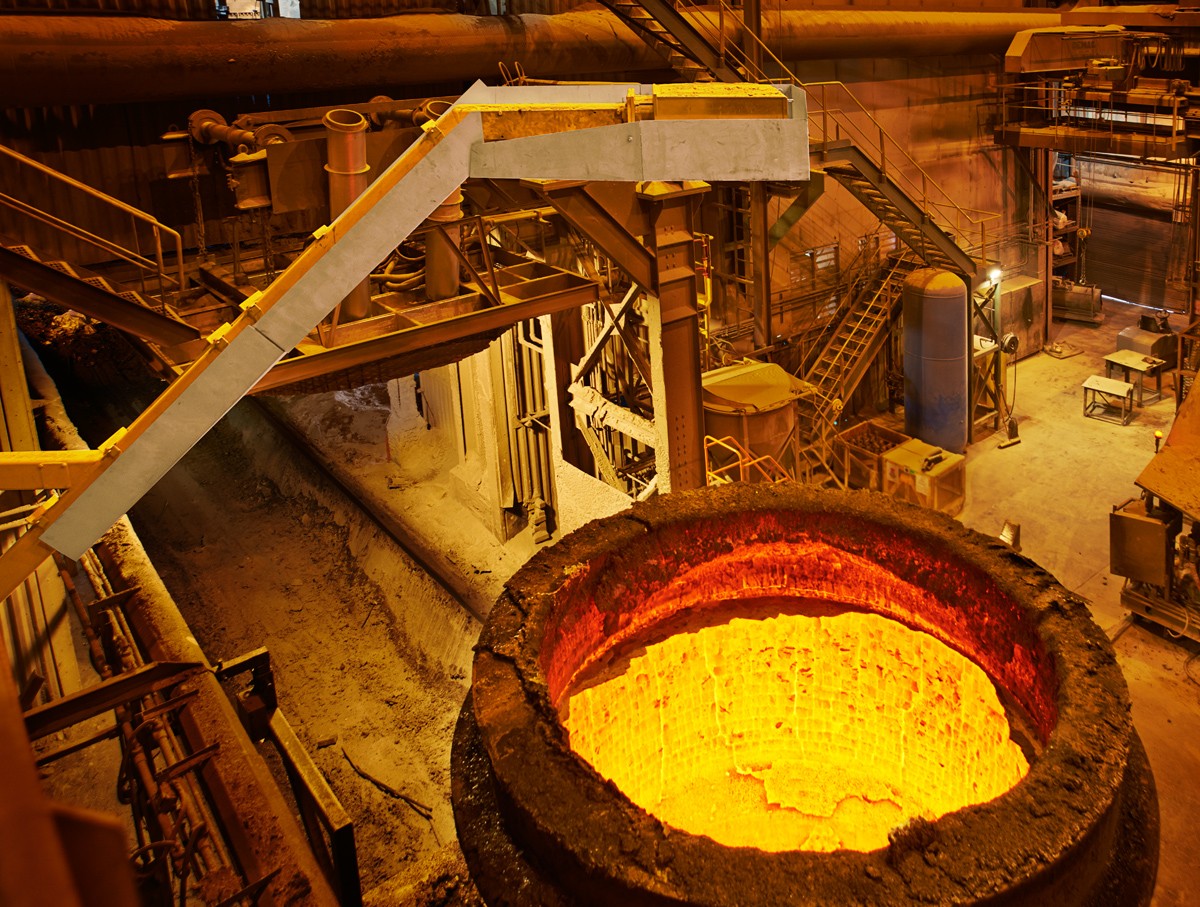
ANTERIS 300c
Container
Whichever location is right for a fixed laser ladle project, if it does not require an arm and time is tight, then the ANTERIS 300c is a easy and clean way to speed-up installation in this self-contained solution.
The shipping box is used as the enclosure of the laser unit. All components are pre-tested at the factory and the few connections to the plant (all fluids and signal) can be made quickly as soon as the box is bolted in its final position. The best solution for projects with tight deadlines or short shut-downs!
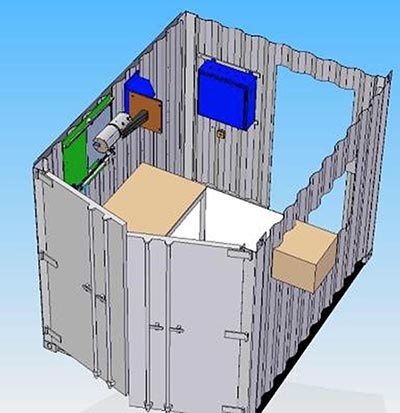
ANTERIS 300s
Laser Guided Gunning – Spray control
Includes the thickness measurement and the GUI [graphical user interface] to control the robot.
Vesuvius and its partners can offer a fully automatic refractory management system including thickness measurement and repair for all vessel types.
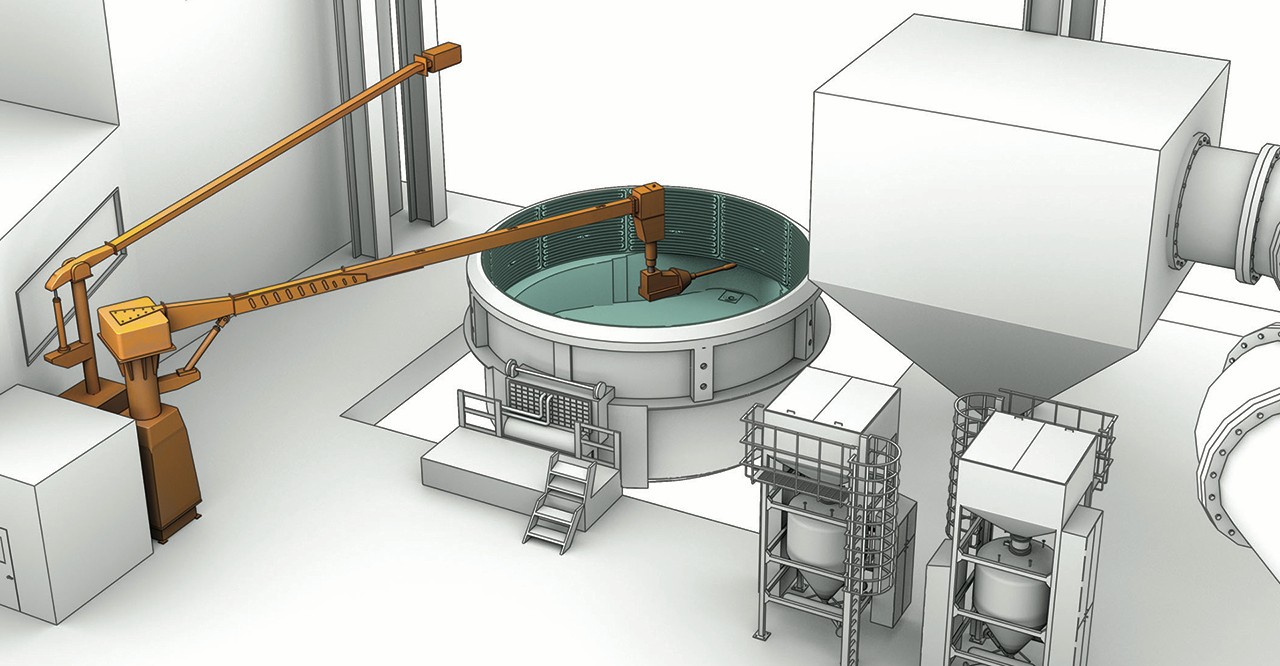
ANTERIS 300dm
Door mounted for BOF applications
BOF plants which have tight schedules and want to improve both safety and productivity have a keen interest in this product. The door-mounted unit may not work for all door types, but when they do the results are outstanding.
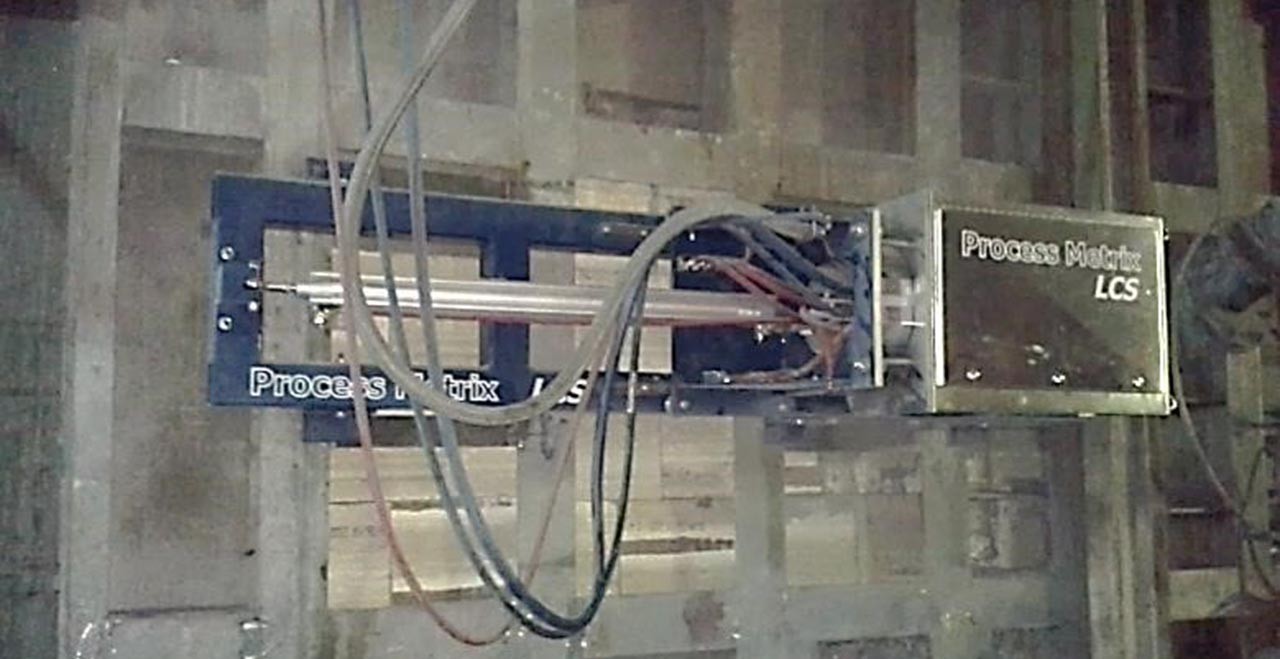
ANTERIS 300i
Insert-able System
For BOF plants with tightest requirements in terms of safety and productivity, the insertable system will provide a safe measurement in a single scan for the shortest turn-around time.
For Ladle systems, this technology is applicable in all circumstances. However, it is most relevant to steel plants where the skull build-up over the lip is so large that a large portion of the wall would be missed if scanned by a regular fixed unit.
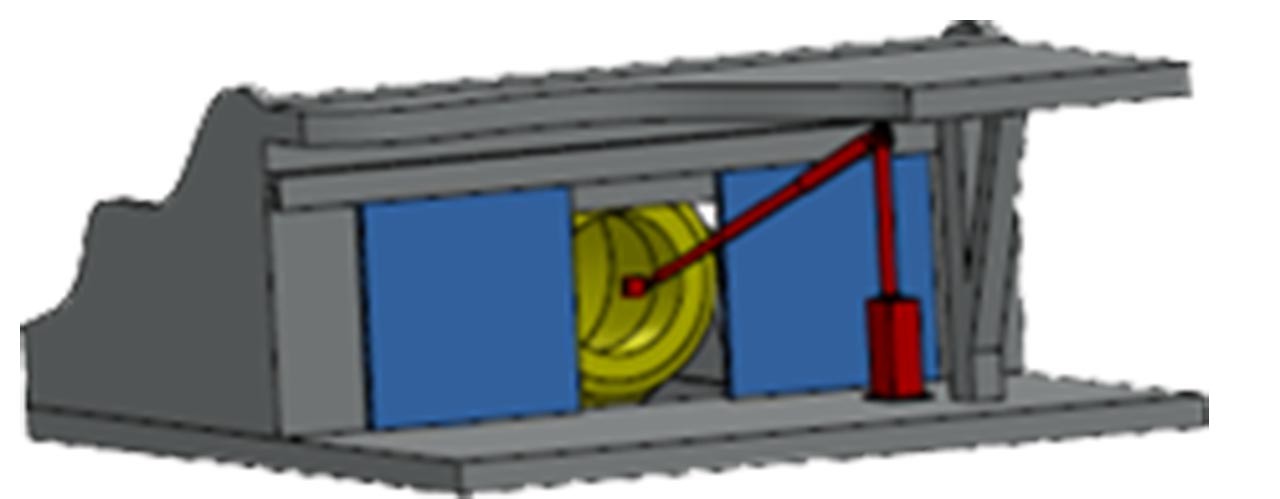
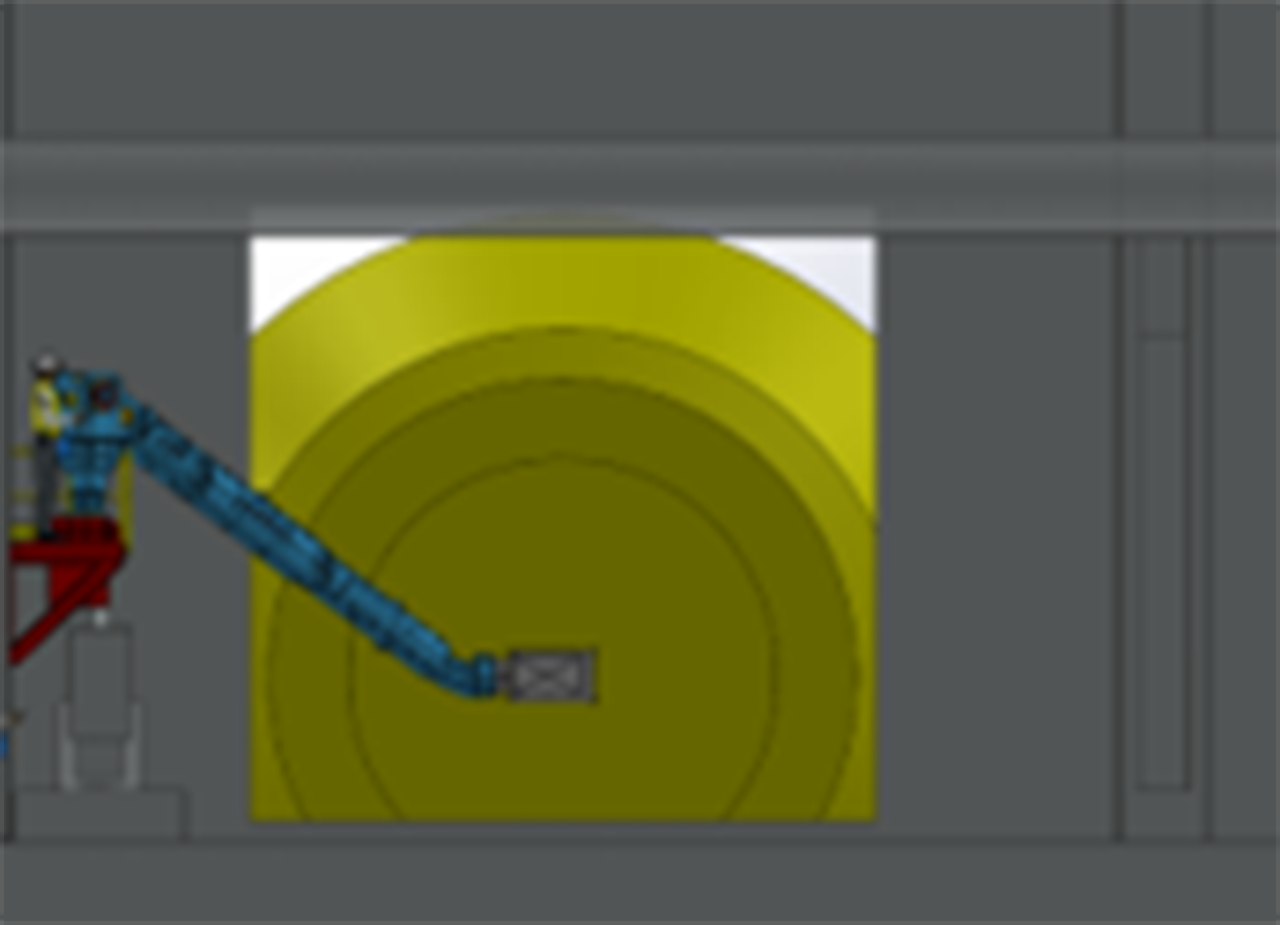
ANTERIS 300it
Torpedo car applications
The ANTERIS 300it is a version of ANTERIS 300i dedicated to the measurement of Torpedo Ladles refractory thickness. Our flexible approach to the is unique challenge will be the key to a successful Torpedo Ladles refractory management program.
