Inclusions and Impurities in molten steel
From the steel
- Chemical elements
Fe, Mn, Si, Al, Ti, Cr… - Native inclusions
Contact with the boundary layer depends on number of casting flow - Inclusions formed by cooling
Formed at the refractory surface - Inclusions from reoxidation
On the refractory surface - The healing
The deoxidizer is trying to take over the slag
From the refactory
- Permeability (Porosity)
Path for gases H2O, O2, Air, SiO, CO, N2 - Degassing
Result of refractory composition
C + SiO2 → SiO + CO
C + MgO → Mg + CO - Active components
Silica
Protective metals Al, Al-Mg - Part of everyday process: Gaskets/mortar joint
Large path for air
Site of intense reoxidation
Often result in a breakout
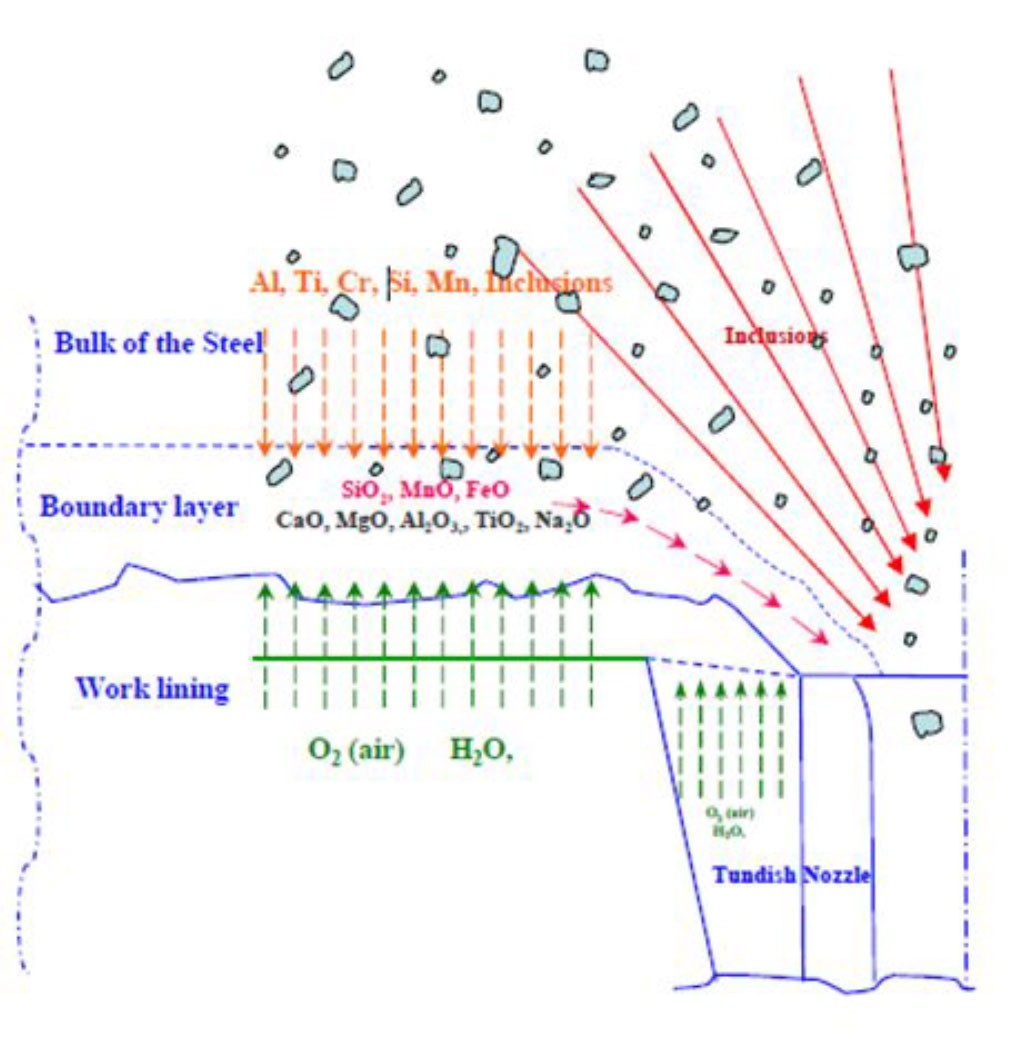
Map of inclusions and impurities in molten steel.
Tundish working lining materials
Calcia - CaO
Very stable oxide
Violently hygroscopic
Reactive with Al2O3 and can form low melting calcium aluminate compounds
Not a good candidate for most steel making operations
Silica – SiO2
Low melting point
Very susceptible to softening at steel temperatures when steel impurities are present
Can react with metallurgical components in the steel (Al, Ti, Mn) leading to re-oxidation
Mainly used as backing material behind tundish boards and as a base for older generation pre-shaped boards
Magnesia - MgO
Stable Oxide
Melting point of pure MgO is very high allowing a high tolerance for residual compounds (impurities)
Allows working linings to be made with lower purity.
MgO compounds, such at Olivine, can lead to the formation of spinel
Spinel is the “glue” that allows inclusions to increase in size which can lead to SEN clogging and surface defects
Currently the most popular material of choice for use in Tundish working linings
Alumina – Al2O3
Chemically pure
High density and low porosity
Low reactivity with residual components in steel metallurgy
Significant reduction in oxygen potential of the Tundish lining system
Removal of MgO prevents Spinel formation.
Spinel is the “glue” that allows inclusions to increase in size which can lead to SEN clogging and surface defects.
Optimized inclusion reduction - Next generation Tundish Working Lining SUPERGARD
Tundish Lining Development – Products and Materials
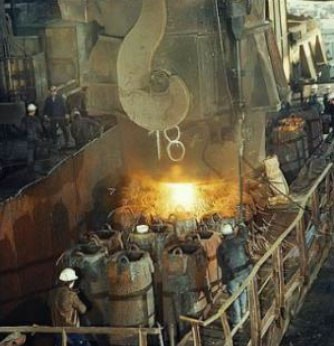
Ingot Casting
→ Evolution →
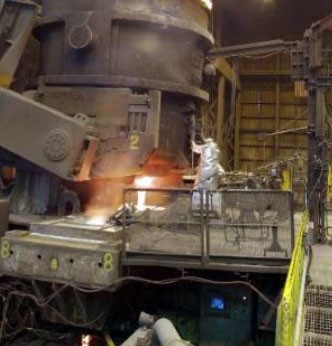
Continuous Casting
The Casting process evolved from ingot casting to continuous casting
Product types
Bricked Tundish Lining
Pre-shaped Tundish Boards
Trowelable Tundish Lining
Gunnable Tundish Lining
Dry Vibratable Tundish Lining
Sprayable Tundish Lining
Product types have evolved from bricks to spray and dry-vibratable
Materials
Calcia - CaO
Silica – SiO2
Magnesia - MgO
Alumina – Al2O3
Tundish Lining Material technology has evolved from zirconia to alumina
Evolution
SUPERGRAD (Spray Mix)
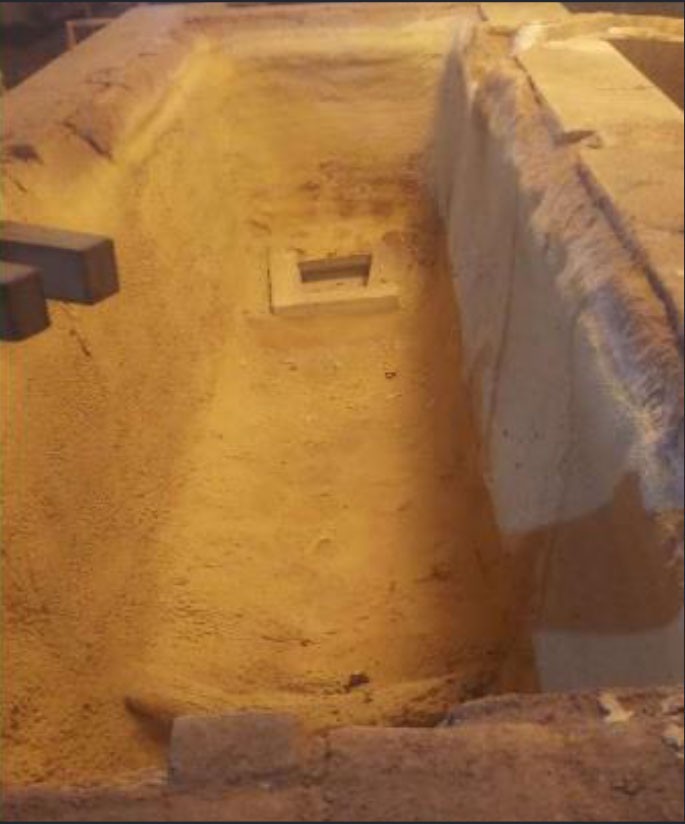
SUPERGARD OBL is the combination of the highest purity materials with advanced installation technology
SUPERGARD: Vesuvius new application technology
A superior working lining alumina-based product with low reactivity at steel casting temperatures, specifically developed to reduce inclusion formation in the Tundish during casting operations.
Features
Extremely high purity / low reactivity lining
Low oxygen permeability (barrier concept)
High density
Low steel wettability
Advantages
Reduced clogging of the upper tundish nozzle
Provides erosion-corrosion resistance
in working line.Reduced slab defects.
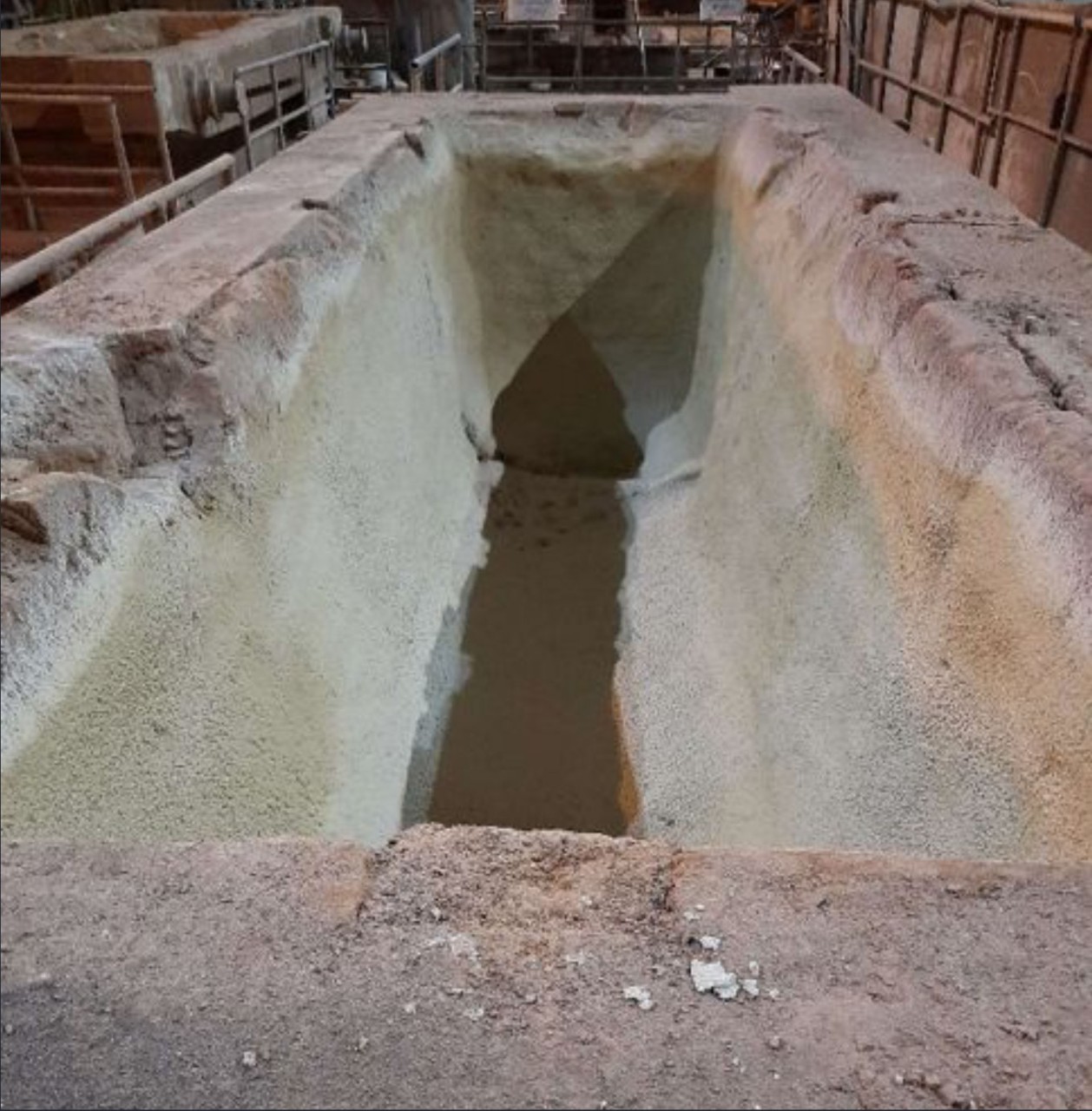
SUPERGARD OBL - Installation
Installation steps:
01.
Apply the first layer
of standard working lining (BASILITE*)
02.
Apply a 15-20 mm thick layer of SUPERGARD OBL via the same spray machine over BASILITE spray
03.
Single dry-out cycle
is required.
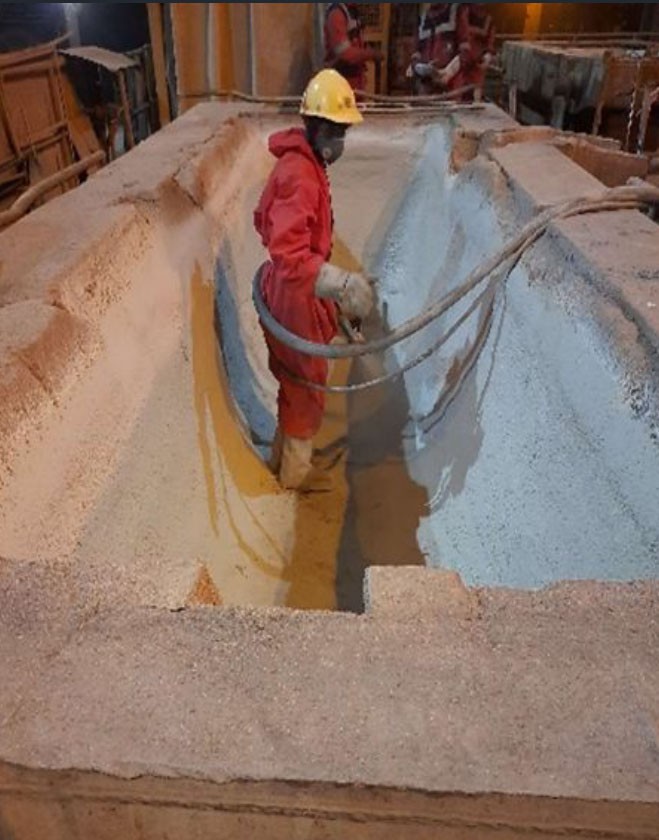
SUPERGARD OBL installation
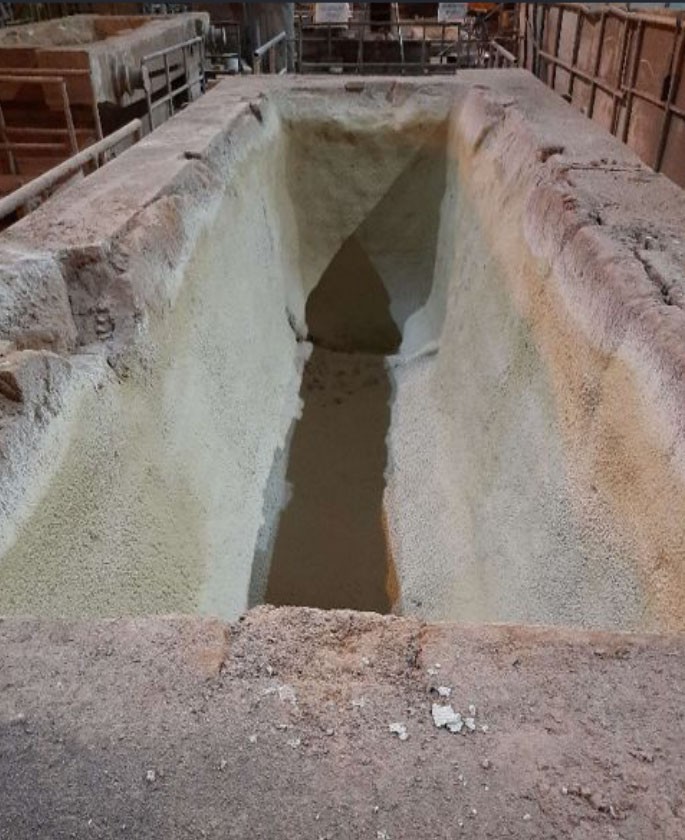
Tundish after completion of spray and before dry-out
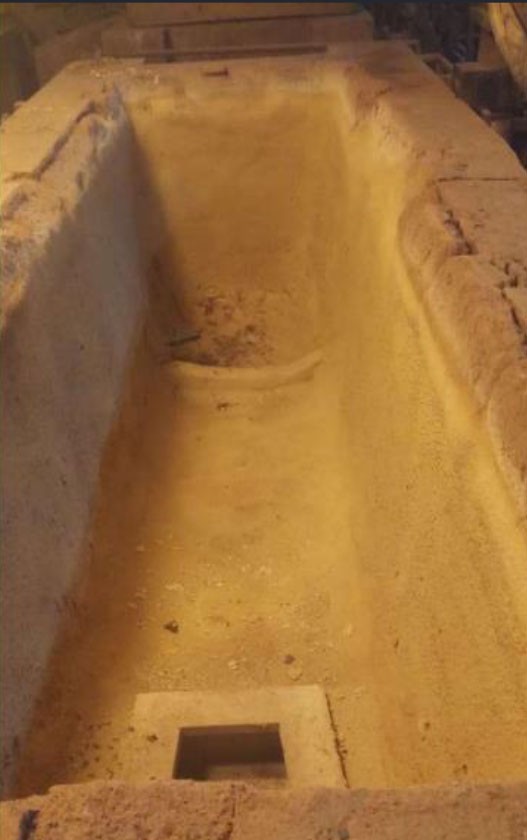
Tundish after dry-out
How the SUPERGARD OBL Lining works
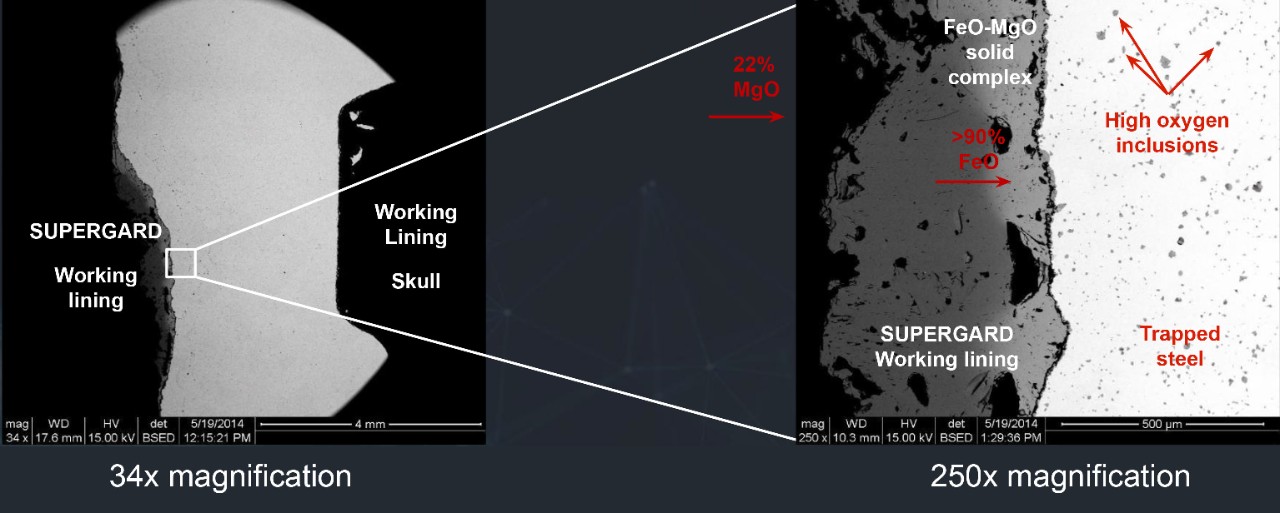
A field trial of basic working lining and SUPERGARD OBL lining shows high concentration of oxygen inclusion in the steel trapped between the two linings.
Results of using SUPERGARD OBL
Working lining
8500 oxide inclusions
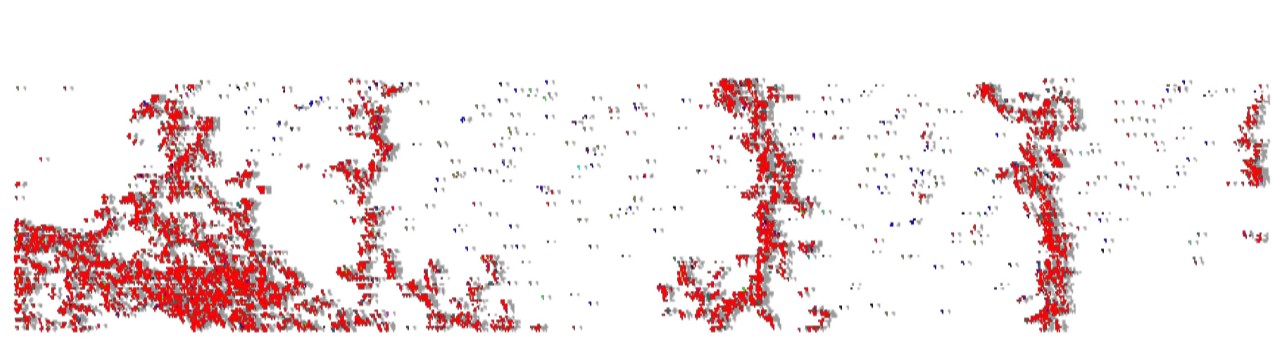
SUPERGARD OBL lining
4000 oxide inclusions
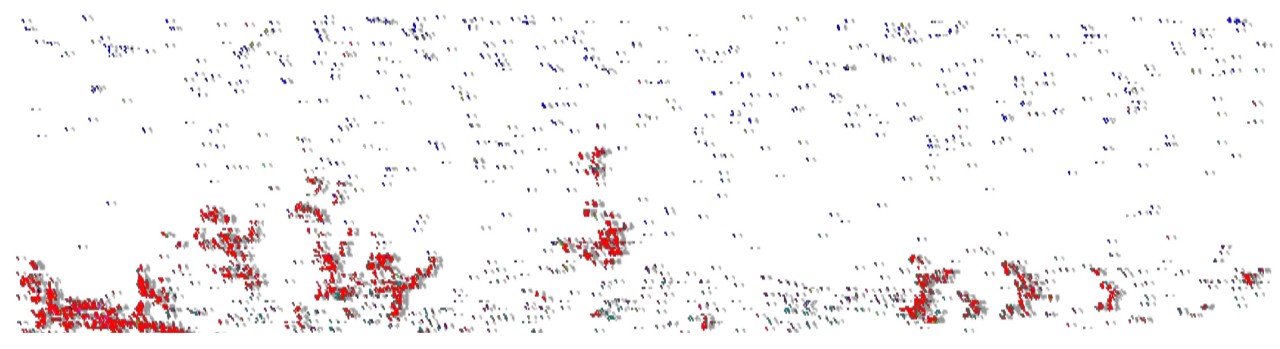
Conclusion: 8.500 oxide inclusions compared to 4.000 oxide inclusions with SUPERGARD shows a massive reduction in inclusions on steel surface – improvement of greater than 50%!
Results of using SUPERGARD OBL technology
Initial success with SUPERGARD OBL application Significant reduction in rejected coils
6 month utilization of SUPERGARD OBL on entire tundish
Over 50% improvement on Lamination/Sliver retreats.
Over 25% improvement on Lamination/Sliver losses
50% reduction in the need for rodding from above the tundish (removing the alumina bridging from wells)
SUPERGARD OBL is an extremely high purity lining barrier for the reduction of re-oxidation in the tundish and SEN clogging with a distinctive impact in steel casting and slab quality.
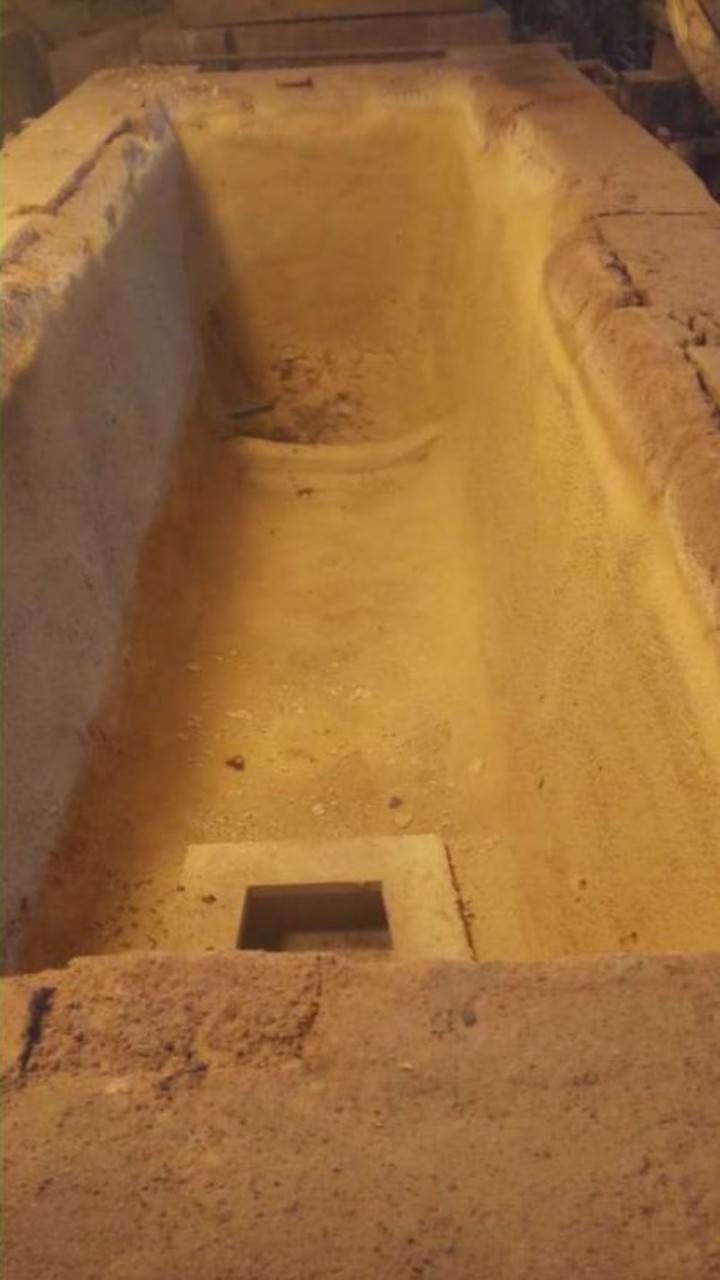
SUPERGARD readily installed
SUPERGARD OBL
Tundish Working Lining for High Quality Steel
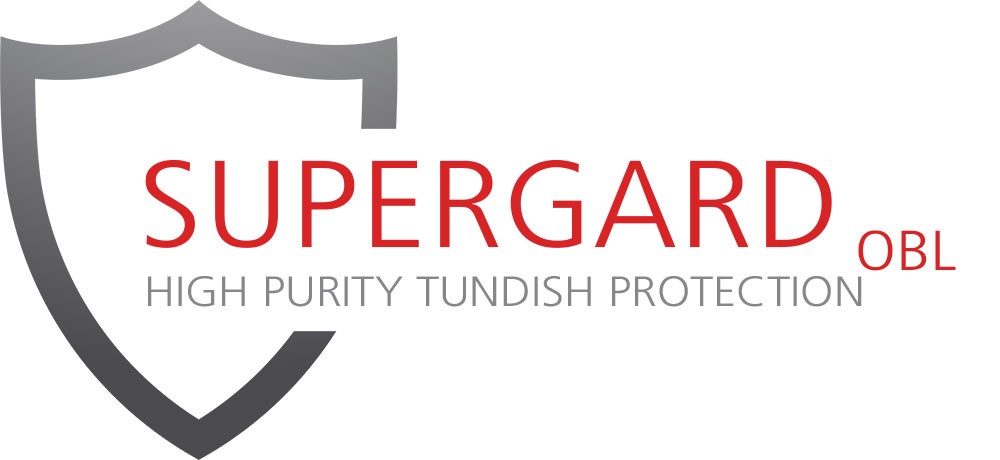