Controlling the flow of steel from the tundish to the mould is very important for Beam Blank Casters. It strongly contributes to the ability to produce the optimum steel quality with the maximum caster safety.
Achieving the highest steel quality and caster productivity requires:
- a precise and reliable control of the molten steel that guarantees a stable, level meniscus
- an optimized introduction and distribution of steel in the very specific Beam Blank mould shape.
- an appropriate formulation and consistent distribution of mould flux
Vesuvius brings its skills and experience to develop and service cutting edge solutions that maximize production quality and throughput with the highest level of safety. The integration of Avemis, Sert Metal and Metallurgica enlarged the Vesuvius portfolio and experience in this field.
Solutions are available for tundishes equipped with either slide gates, stoppers or calibrated nozzles.
Shroud
VISOTM Shroud : Tundish to Mould shrouding

Primary function and objectives of the shroud:
- controlled submerged entry and distribution of molten steel from tundish to mould
- thereby preventing reoxidation of the steel and improving quality
Main features:
- Isostatically pressed tube (VISO™),
- Tailored to each individual requirement and condition through :
- Vesuvius flow modelling expertise and global facilities
- Vesuvius refractory material expertise.
- Depending on caster specific flow control system, the shroud can be:
- SEN: one piece Submerged Entry Nozzle
- SES: two pieces Tundish Nozzle and Submerged Entry Shroud
Level Control
AMLC: Automatic Mould Level Control and associated flow valve refractories
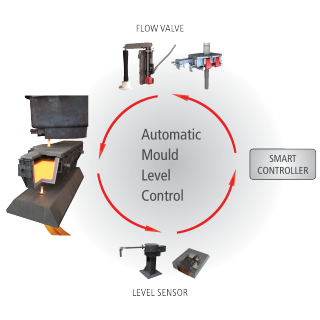
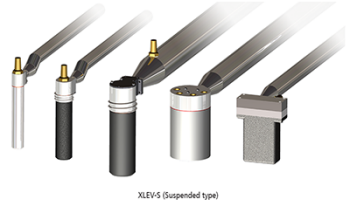
Extensive Flow Valve offering
Primary objectives:
- Provide accurate and fast flow control adjustment from tundish to mould
- In some cases, be flexible to operate the same caster either with a flow control valve or with a calibrated nozzle & calibrated nozzle changer.
Main features:
- Availability of different flow valve designs that will cover all casters needs
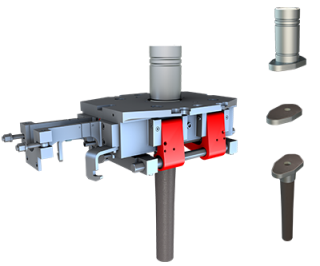
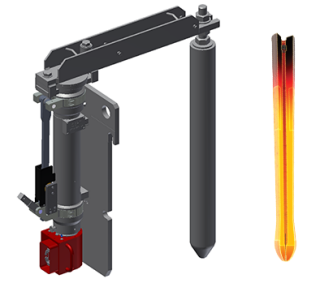
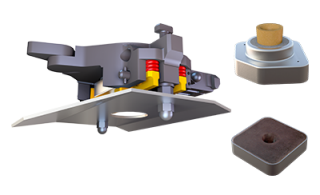
Smart Mould Level Controller
Primary objectives:
- Drive the flow valve to minimize meniscus deviation
- Self-adapt to perturbations in process
Main features:
- Decide in real time the best control strategy along casting sequence
- Minimize meniscus fluctuation when strong perturbations occur
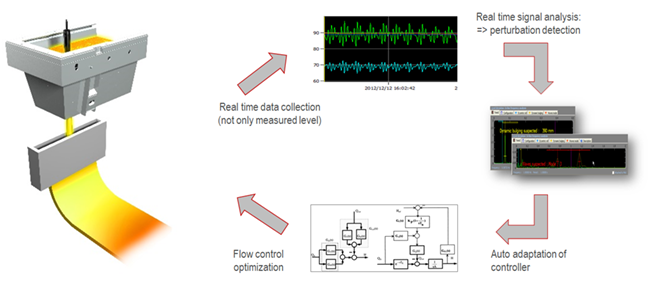
Gas Inerting
Inert Gas Control for steel protection
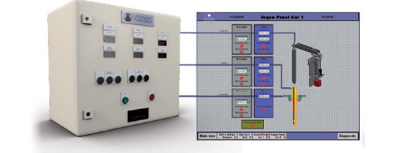
Primary objectives:
- Management of inert gas application to reduce risk of air ingression
Main features:
- Multi-channel control panel, using mass flowmeters
- Double line per loop with back pressure measurement (option)
- 3 operating modes (option): Automatic Flow Control, Automatic Pressure Control, Manual
Flux Powder
Flux Powders and Distribution Mechanisms
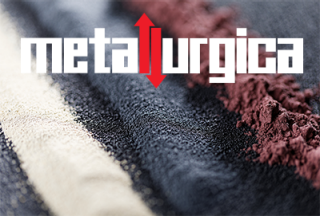
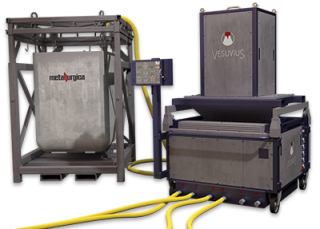
Primary objectives:
- Create lubrication layer between steel shell and mould faces,
- Protect steel top surface from re-oxidation and heat loss,
- Control heat transfer between strand & mould,
- Capture inclusions floating to top surface
- Distribute the flux regularly over the steel surface